About Alcast Company
Table of ContentsSome Ideas on Alcast Company You Should KnowThe 5-Minute Rule for Alcast CompanyAlcast Company Fundamentals ExplainedFacts About Alcast Company RevealedLittle Known Questions About Alcast Company.The Buzz on Alcast Company
Chemical Contrast of Cast Light weight aluminum Alloys Silicon advertises castability by minimizing the alloy's melting temperature and improving fluidity throughout casting. Furthermore, silicon contributes to the alloy's strength and put on resistance, making it important in applications where toughness is critical, such as vehicle components and engine elements.It likewise improves the machinability of the alloy, making it much easier to refine into finished products. In this method, iron contributes to the general workability of aluminum alloys.
Manganese adds to the strength of light weight aluminum alloys and boosts workability. Magnesium is a lightweight aspect that supplies strength and impact resistance to aluminum alloys.
Alcast Company Can Be Fun For Anyone
Zinc boosts the castability of light weight aluminum alloys and assists control the solidification procedure during spreading. It enhances the alloy's strength and firmness.
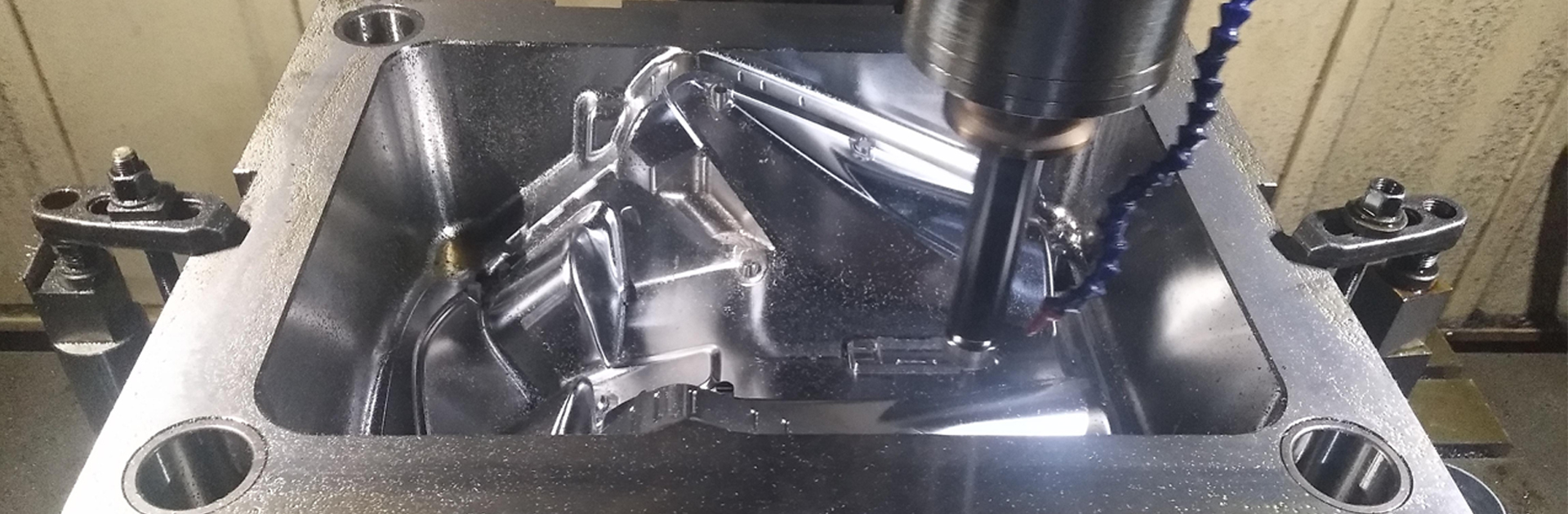
The key thermal conductivity, tensile toughness, yield toughness, and prolongation differ. Amongst the above alloys, A356 has the highest thermal conductivity, and A380 and ADC12 have the lowest.
6 Simple Techniques For Alcast Company
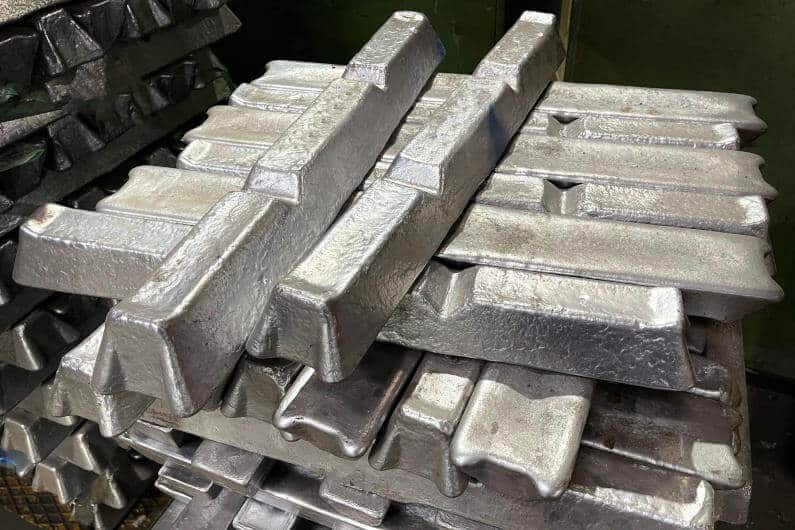
In precision spreading, 6063 is well-suited for applications where detailed geometries and top quality surface area coatings are vital. Examples include telecommunication enclosures, where the alloy's remarkable formability enables sleek and cosmetically pleasing styles while preserving structural integrity. Similarly, in the Lighting Solutions industry, precision-cast 6063 components create classy and effective lighting components that call for intricate shapes and excellent thermal performance.
It causes a better surface finish and much better deterioration resistance in A360. The A360 displays exceptional prolongation, making it suitable for complex and thin-walled parts. In accuracy spreading applications, A360 is well-suited for markets such as Consumer Electronics, Telecommunication, and Power Devices. Its improved fluidity enables for detailed, high-precision components like smartphone housings and communication tool housings.
The 30-Second Trick For Alcast Company
Its unique residential or commercial properties make A360 a valuable choice for precision spreading in these markets, boosting product toughness and top quality. Light weight aluminum alloy 380, or A380, is a widely used spreading alloy with numerous unique features. It offers excellent castability, making it an excellent selection for precision spreading. A380 exhibits excellent fluidness when molten, guaranteeing elaborate and in-depth molds are precisely recreated.
In accuracy spreading, aluminum 413 radiates in the Customer Electronic Devices and Power Equipment markets. click to investigate This alloy's premium deterioration resistance makes it an outstanding option for outdoor applications, making sure durable, long lasting products in the discussed markets.
The Buzz on Alcast Company
Once you have determined that the light weight aluminum die casting procedure is suitable for your project, an essential following step is deciding on the most appropriate alloy. The light weight aluminum alloy you choose will significantly impact both the casting process and the homes of the end product. As a result of this, you must make your decision very carefully and take an educated approach.
Establishing the most appropriate aluminum alloy for your application will indicate considering a wide array of features. The first category addresses alloy qualities that affect the manufacturing process.
Some Known Details About Alcast Company
The alloy you pick for die spreading directly affects numerous facets of the spreading process, like how easy the alloy is to function with and if it is prone to casting flaws. Warm fracturing, likewise referred to as solidification cracking, is a normal die casting defect for light weight aluminum alloys that can cause internal or surface-level tears or fractures.
Certain aluminum alloys are more prone to warm cracking than others, and your choice ought to consider this. It can harm both the actors and the die, so you must look for alloys with high anti-soldering buildings.
Deterioration resistance, which is currently a noteworthy feature of light weight aluminum, can vary considerably from alloy to alloy and is a necessary particular to think about depending on the environmental conditions your item will be subjected to (aluminum foundry). Put on resistance is an additional home commonly looked for in light weight aluminum items and can separate some alloys